Engineering Analysis of a Dowel Pin:
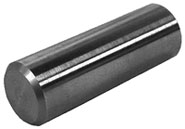
Tolerance Stack-Ups
A 3D CAD model is designed to the nominal dimension (or “nom”), but it will be manufactured to a tolerance. A simple pin will have a Max and Min diameter and length. This tolerance has to be considered when designing mating parts…the Min diameter for the hole must not interfere with the Max diameter of the pin, and so on. With any assembly, we must “stack” up the tolerances of all the relevant parts to ensure that everything will assemble. This can be a tricky matter, but LTS uses state-of-the-art, custom designed engineering tools to manage all of the tolerances to ensure that everything will fit together as intended.
A 3D CAD model is designed to the nominal dimension (or “nom”), but it will be manufactured to a tolerance. A simple pin will have a Max and Min diameter and length. This tolerance has to be considered when designing mating parts…the Min diameter for the hole must not interfere with the Max diameter of the pin, and so on. With any assembly, we must “stack” up the tolerances of all the relevant parts to ensure that everything will assemble. This can be a tricky matter, but LTS uses state-of-the-art, custom designed engineering tools to manage all of the tolerances to ensure that everything will fit together as intended.
Cylindrical Fits
Using the example of a pin, a multitude of possible fit classes can be specified, ranging from a press (interference fit)…to a clearance fit, or somewhere in between. In some cases, the difference in the tolerance of the features for these fits can vary by only a few ten-thousandths (0.0001″) of an inch! Not to mention what happens to the stress on press fit members, and changes to the resulting OD’s and ID’s. LTS has the experience and engineering tools to properly size every cylindrical part so that the final product will work flawlessly.
Using the example of a pin, a multitude of possible fit classes can be specified, ranging from a press (interference fit)…to a clearance fit, or somewhere in between. In some cases, the difference in the tolerance of the features for these fits can vary by only a few ten-thousandths (0.0001″) of an inch! Not to mention what happens to the stress on press fit members, and changes to the resulting OD’s and ID’s. LTS has the experience and engineering tools to properly size every cylindrical part so that the final product will work flawlessly.
Structural Analysis
Maybe our pin will be the hinge for a joint…is it the right size for the job? This, and many other scenarios can be easily determined with hand calculations. All of LTS’s designs are subjected to a rigorous analysis. We know what it takes to create quality, robust designs. Not only do we know all of the equations, we know how, when and why to use them.
Maybe our pin will be the hinge for a joint…is it the right size for the job? This, and many other scenarios can be easily determined with hand calculations. All of LTS’s designs are subjected to a rigorous analysis. We know what it takes to create quality, robust designs. Not only do we know all of the equations, we know how, when and why to use them.
Material Selection
What material should you use for this pin? Tool Steel…Ceramic…Plastic? What heat treatment if its a metal? What does heat treatment even mean? Material analysis is every bit as important as mechanical design. Fortunately, LTS is a materials authority, and will choose the optimal, most cost-efficient material for your product’s requirements. From simple material choices, to alternative material studies, LTS has the resources and knowledge to provide you material solutions.
What material should you use for this pin? Tool Steel…Ceramic…Plastic? What heat treatment if its a metal? What does heat treatment even mean? Material analysis is every bit as important as mechanical design. Fortunately, LTS is a materials authority, and will choose the optimal, most cost-efficient material for your product’s requirements. From simple material choices, to alternative material studies, LTS has the resources and knowledge to provide you material solutions.
Surface Finish
Does the pin need to be chrome plated? Industrial Hard Chrome, not cosmetic (there is a big difference). Perhaps ground and lapped will do. All of these surface finish questions can be answered with proper application of manufacturing processes, and knowledge of component requirements. LTS will specify critical part roughness and surface treatments.
Does the pin need to be chrome plated? Industrial Hard Chrome, not cosmetic (there is a big difference). Perhaps ground and lapped will do. All of these surface finish questions can be answered with proper application of manufacturing processes, and knowledge of component requirements. LTS will specify critical part roughness and surface treatments.
FEA
Finite Element Analysis: when hand calculations just won’t do. If your part has complex geometry, or abnormal loading conditions, or you have multiple parts with dynamic contacts. FEA is a computer simulation that can accurately determine the stress and strain of a part in its service environment. “Can” is the operative word. It takes YEARS of experience to learn how to properly set up and evaluate a FEA study. The consequence of a flawed analysis can be devastating. Your results look good, but could be completely wrong. This could lead to costly redesign, or worse…personal injury. LTS has years of experience in FEA, formal training, and expertise to ensure that you are getting meaningful and accurate results.
Finite Element Analysis: when hand calculations just won’t do. If your part has complex geometry, or abnormal loading conditions, or you have multiple parts with dynamic contacts. FEA is a computer simulation that can accurately determine the stress and strain of a part in its service environment. “Can” is the operative word. It takes YEARS of experience to learn how to properly set up and evaluate a FEA study. The consequence of a flawed analysis can be devastating. Your results look good, but could be completely wrong. This could lead to costly redesign, or worse…personal injury. LTS has years of experience in FEA, formal training, and expertise to ensure that you are getting meaningful and accurate results.
Analytical Modeling
Does your product design have moving parts, complex features like clutches, gearing, motors, cams, or impacting elements? If so, determining if it will actually work can be formidable, even for a seasoned engineer. LTS routinely uses analytical models to simulate the physics of complex, kinematic systems to show the performance and optimize the design. An analytical model is typically an advanced excel spreadsheet, with design controls, animations, and plots that use mathematical formulas to simulate the physics of your design. Just a small list of example simulations that LTS has performed include:
Does your product design have moving parts, complex features like clutches, gearing, motors, cams, or impacting elements? If so, determining if it will actually work can be formidable, even for a seasoned engineer. LTS routinely uses analytical models to simulate the physics of complex, kinematic systems to show the performance and optimize the design. An analytical model is typically an advanced excel spreadsheet, with design controls, animations, and plots that use mathematical formulas to simulate the physics of your design. Just a small list of example simulations that LTS has performed include:
- Clutch Drives
- Transmissions
- Oscillating Joints
- Time-Stepped Runge-Kutta Models
- Impacting Elements
- DC Motor Simulation
- Air and Electric Motors with Resistive Power Sources